당신은 주제를 찾고 있습니까 “reactive ion etching 공정 – Etching Silicon with Plasma – Reactive Ion Etching (RIE)“? 다음 카테고리의 웹사이트 https://dienbienfriendlytrip.com 에서 귀하의 모든 질문에 답변해 드립니다: https://dienbienfriendlytrip.com/finance/. 바로 아래에서 답을 찾을 수 있습니다. 작성자 Sam Zeloof 이(가) 작성한 기사에는 조회수 37,948회 및 좋아요 2,455개 개의 좋아요가 있습니다.
RIE(Reactive Ion Etching)의 원리 장비는 건식 식각장치로 써 마주 보고 있는 두 개의 평행판형 전극에 고주파전 원을 인가하여 플라즈마 상태에서 반응성가스를 활성 화시켜 식각시키고자 하는 물질을 화학반응을 일으켜 휘발성물질로 만들어 식각하는 원리를 이용한다.
reactive ion etching 공정 주제에 대한 동영상 보기
여기에서 이 주제에 대한 비디오를 시청하십시오. 주의 깊게 살펴보고 읽고 있는 내용에 대한 피드백을 제공하세요!
d여기에서 Etching Silicon with Plasma – Reactive Ion Etching (RIE) – reactive ion etching 공정 주제에 대한 세부정보를 참조하세요
https://twitter.com/szeloof
OUTLINE:
0:00 – intro
1:10 – chamber overview
2:26 – etch demo
3:58 – demo results
5:40 – endpoint detection
7:37 – quirks, subtleties, safety
10:39 – construction
Music is shanghai by king gizzard and the lizard wizard
reactive ion etching 공정 주제에 대한 자세한 내용은 여기를 참조하세요.
Reactive Ion Etching, RIE 공정에 대해서 설명하세요
ion assisted etch라고 부르기도 합니다. RIE 공정은 물리화학적 방법을 사용한 식각방법으로, 화학적 식각을 보조하기 위해 물리적 방법을 활용하거나, …
Source: sshmyb.tistory.com
Date Published: 8/3/2021
View: 2098
반도체 공정 5 : 식각 공정(Etching process) 2편
RIE (Reactive Ion Etch)는 화학적 식각(Gas phase etch) 물리적 식각(Sputtering)을 결합하여 사용하는 건식 식각입니다. 원리는 간단합니다. 플라즈마에 …
Source: numong22.tistory.com
Date Published: 1/20/2022
View: 4970
[반도체 특강] 식각(Etching), 패턴을 완성하다-下
RIE 방식의 핵심은 이방성인 양이온으로 식각 부위를 공격해 막질 내 타깃의 분자-분자 간 결합력을 약화시킨 뒤 약해진 부위를 라디칼이 흡착, 막을 구성 …
Source: news.skhynix.co.kr
Date Published: 2/5/2022
View: 7013
RIE(Reactive Ion Etching)에 대해 알아보기(feat. 플라즈마의 …
Reactive Ion Etching(이하 RIE)는 보통 Fluorine(F)에 13.56MHz(Radio Frequency)를 가해서 플라즈마 이온으로 만듭니다.(다른 frequency도 가능하지만 13.56MHz가 제일 …
Source: jista.tistory.com
Date Published: 8/27/2022
View: 9734
Reactive Ion Etching – MKS Instruments
Reactive Ion Etching (RIE) uses a combination of chemical and physical reactions to remove material from a substrate; it is the simplest process that is …
Source: www.mks.com
Date Published: 2/12/2021
View: 4071
Reactive-ion etching – Wikipedia
Reactive-ion etching (RIE) is an etching technology used in microfabrication. RIE is a type of dry etching which has different characteristics than wet …
Source: en.wikipedia.org
Date Published: 8/23/2022
View: 1180
주제와 관련된 이미지 reactive ion etching 공정
주제와 관련된 더 많은 사진을 참조하십시오 Etching Silicon with Plasma – Reactive Ion Etching (RIE). 댓글에서 더 많은 관련 이미지를 보거나 필요한 경우 더 많은 관련 기사를 볼 수 있습니다.
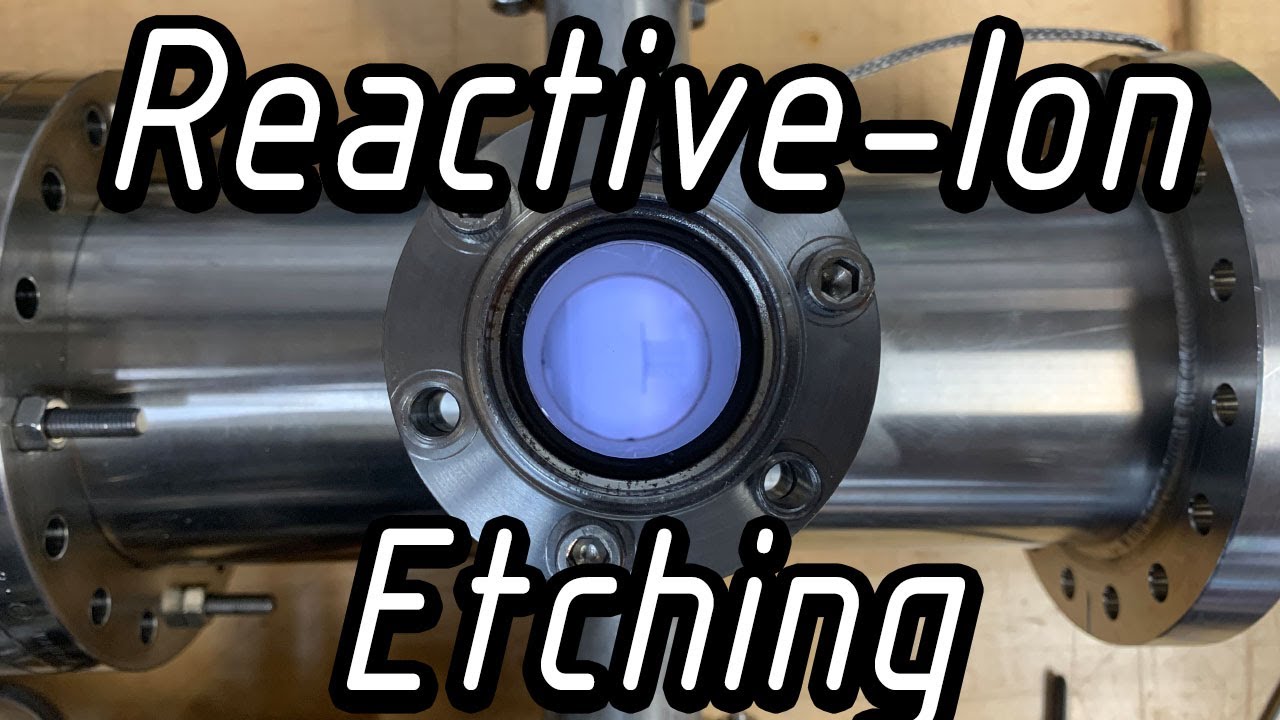
주제에 대한 기사 평가 reactive ion etching 공정
- Author: Sam Zeloof
- Views: 조회수 37,948회
- Likes: 좋아요 2,455개
- Date Published: 2021. 6. 27.
- Video Url link: https://www.youtube.com/watch?v=RoQgnC0Oz2k
[제이벡] RIE
반응성 이온 식각(RIE)은 이온 충격을 이용한 반응성 화학 공정과 물리적 공정에서 웨이퍼표면으로부터 물질을 제거하기 위한 기술이다.
웨이퍼가 RF가 인가되는 전극(cathode)에 위치하는 것을 제외하고는 평행평판(parallel-plate)플라즈마 식각기와 비슷하고 전압이 가해진 전극의 크기는 접지된 전극의 크기에 비해 크게감소된다.
이런 방식에서 직류 자기 바이어스가 캐소드에서 발생되고 웨이퍼들은 플라즈마에 대한커다란 전압 차를 얻게 된다.
이러한 상태는 이온화된 species들이 웨이퍼를 향해 움직이도록하는 방향성을 만들어내고, 향상된 이방성의 측벽 특성을 만들어낸다.애노드에는 스퍼터링이 없다.
압력은 0.1torr 이하로 비교적 낮다. RIE(Reactive Ion Etching)의 원리 장비는 건식 식각장치로 써 마주 보고 있는 두 개의 평행판형 전극에 고주파전 원을 인가하여 플라즈마 상태에서 반응성가스를 활성 화시켜 식각시키고자 하는 물질을 화학반응을 일으켜 휘발성물질로 만들어 식각하는 원리를 이용한다.
고주파 전원의 인가전극에 웨이퍼가 놓이는 Cathode-couple방식은 접지전극측에 웨이퍼가 놓이는 Anode-couple방식보다 인가전압이 크므로 높은 이온충격을 이용할 수 있는 특징이 있는 장치이다.
반응성 가스의 플라즈마에 존재하는 활성종을 에칭재료 표면의 원자와 반응시켜 휘발성의 반응생성물을 생성시키고, 이것을 재료 표면에서 이탈시켜 에칭하는 기술이다.
이 기술은 반도체 소자 초미세 가공과정의 기본기술로 확립되어 있다.RIE 기술은 보통 크리닝, 디스컴등에 사용을 하며, 여러종류의 필름(전도성, 유전성)을 에칭한다.
[출처] Dry Etch(건식 식각) 장비 종류 – RIE|작성자 햇살마루
[식각공정] 훈련 4 : “Reactive Ion Etching, RIE 공정에 대해서 설명하세요”
반응형
오늘은 Plasma etching인 Reactive Ion Etch, RIE 공정 메커니즘에 대해서 다루어보도록 하겠습니다.
[질문 1]. Reactive Ion Etching, RIE 공정에 대해서 설명해주세요. RIE는 Reactive Ion Etching으로 High plasma etching과 ion milling 두 에칭 공정의 장점을 한 데 모은 것이라고 생각할 수 있습니다. ion assisted etch라고 부르기도 합니다. RIE 공정은 물리화학적 방법을 사용한 식각방법으로, 화학적 식각을 보조하기 위해 물리적 방법을 활용하거나, 화학적 식각에 관여하는 etchant 반응물질을 생성하기 위해 물리적 방법이 사용됩니다. Self bias effect에 의해 cathode sheath가 형성되고, sheath voltage에 의해 이온들이 target 박막으로 가속되어 vertical profile 구현이 가능해집니다. 정리하자면, plasma를 통해 이온화된 반응성 gas와 plasma 내 양이온의 ion bombardment를 모두 활용하는 방법으로 각각의 방법들의 단점을 보완하는 빠른 비등방성 식각과 높은 etch selectivity를 가지는 공정입니다. [꼬리 1-1]. RIE의 메커니즘에 대해서 설명해주세요. RIE의 메커니즘은 크게 6가지로 구분할 수 있습니다. 먼저 ① glow discharge에 의해 plasma가 형성됩니다. plasma 내의 양이온과 radical이 RIE 메커니즘에 기여 한다고 할 수 있습니다. ② plasma 내의 etchant 물질이 확산되어 target 표면으로 이동합니다. ③ 표면으로 이동한 etchant 물질은 target 표면에 흡착되고, ④ 양이온 충돌(ion bombardment)로 분자간 결합이 약해진 영역은 흡착된 etchant 물질과 쉽게 반응하여 휘발성 화합물을 생성합니다. ⑤ 생성된 화합물들은 표면으로부터 탈착되고, ⑥ 확산에 의해 기체 층으로 이동하고, 진공장비에 의해 배출됩니다.
[꼬리 1-2]. RIE 공정의 selectivity 특성에 대해서 설명해주세요.
RIE etching은 플라즈마 상태의 이온들이 substrate에 빠른 속도로 부딪혀 physical etching (ion bombardment)를 일으키거나 화학적 반응을 수반하는 chemical etching이 한 순간에 일어납니다. Fluorocarbon gas (CFx)를 plasma 상태로 만들어 etching 한다고 가정했을 때, RF power를 약하게 인가할 경우, self bias effect가 작아 낮은 sheath 전압이 형성되어 양이온들이 작은 에너지로 기판과 충돌합니다. 이러한 경우, 반응 etchant 물질이 표면에 흡착되어 쌓이는 속도가 크기 때문에 전체적으로 봤을 때, fluorocarbon이 deposition이 됩니다. CFx가 쌓이면 polymer를 형성하고 C3F6가 CF3, C2F6보다 더 많이 증착됩니다. 여기서 수소 gas가 함께 첨가되면 H는 증착된 CFx와 반응하여 HF를 만들어 반응에 참여하지 못하게 함으로써 F/C ratio가 낮아지면서 chemical etch rate가 감소하게 됩니다. 여기서 높은 RF power를 인가할 경우, 높은 self bias effect에 의해 sheath voltage가 커지고, 특정 threshold voltage를 넘게 되면서 이온 충돌에 의한 etching이 일어납니다. Chemical etch rate을 이와 같이 제어할 수 있기 때문에 RIE 공정에서는 vertical profile을 구현할 수 있는 것입니다.
[세부설명]
RIE 공정 내에서 이온충돌에 의한 Sputtering 식각은 고속으로 가속된 양전하의 충돌에 의해 발생합니다. 적은 양의 음전하 이온은 플라즈마를 형성하면서, 웨이퍼 표면에 도달하지 않고 실질적인 플라즈마 식각에 관여하지 않습니다. 양이온의 경우 이방성 식각의 특징을 가지지만, Selectivity가 낮고, 이온 충돌에 의해 손상될 수 있습니다.
RIE 공정 내에서 radical에 의한 순수한 화학적 식각이 포함됩니다. target 표면에 흡착하여 화학적 반응을 통해 휘발성 화합물을 생성하고 탈착됩니다. 높은 etch rate와 우수한 selectivity를 가지지만, 작은 이온 충돌로 손상이 발생할 수 있으며, 등방성 식각의 특징을 가집니다.
이러한 물리화학적 식각이 적절하게 동시에 일어나면서 이방성 특징을 가지며, 우수한 selectivity와 적당한 이온 충돌에 의한 손상을 가지게 됩니다.
[꼬리 1-3]. RIE에서 End of point, EOP는 어떻게 구별하는지 설명해주세요.
대부분의 플라즈마 공정은 적외선에서 자외선 파장 범위의 빛을 방출합니다. 이 빛의 파장은 원자의 고유 성질이므로 플라즈마에서 방출하는 광의 파장을 분석하면 어떤 물질이 Etching되었는지 확인할 수 있습니다. EOP는 이러한 원리가 적용된 방법입니다. Dry etching의 경우 target 박막의 하부막에 대한 selectivity가 낮기 때문에, EOP를 설정하는 방법이 wet etching과는 다릅니다. 그래서 etching 공정의 종료를 감지하는 EOP 측정 시스템이 요구됩니다. 종점을 정의하거나, etch rate을 지속적으로 모니터링 할 때는, 웨이퍼 표면에서의 레이저 간섭을 이용합니다. 각 층의 바깥쪽 경계면에서 반사된 빛과 안쪽 경계면으로 반사된 빛의 간섭에 의해 식각할 동안 표면 박막에서 반사된 레이저 빛의 강도는 진동하게 됩니다. 따라서 식각의 종점을 반사율의 진동의 정지로 파악할 수 있습니다.
위 그림은 Silicide와 poly-Si gate의 식각 신호를 나타냅니다. Poly-Si의 첫번째 종점에서 Peak이 반만 나타났기에 0.5 나머지는 3개의 peak이 완전하게 발생했기 떄문에 1로 생각하면 총 3.5번의 식각이 나타난 것을 확인할 수 있습니다.
[질문 2]. Etch 공정에서의 Chemistry에 대해서 설명하세요.
Etch 공정에서 사용하는 Gas는 주로 얼마나 화학적 반응을 잘 일으키는지 초점을 둡니다. 그래서 Etching 공정 시 사용하는 대부분의 Etchant Gas는 F, Cl, Br이 화학적 반응을 담당하며 이를 ‘Main Gas’라고 합니다. 그리고 Plasma를 형성하기 위해 추가적으로 O2, N2, He, Ar 등이 ‘첨가 가스’로 사용됩니다. Main Gas인 Etchant Gas를 사용하여 Etching 할 때에는 항상 Byproduct가 생성됩니다. 그래서 Gas의 구성을 어떻게 하냐에 따라 Etch 특성을 쉽게 결정할 수 있습니다. Etch Rate이나 Etching 이후 Profile은 Byproduct에 따라 결정된다고 할 수 있습니다.
[Etch 공정에서의 Plasma]
Plasma Etching을 하기 전에 우선 Plasma를 형성해야 합니다. Plasma는 PVD 공정에서 자세하게 다루었으니 참고 바라겠습니다. Plasma는 전극에 Bias를 인가하여, Glow Discharge를 통해 발생하는 기체의 준중성 상태를 말합니다. 앞서 말씀드린 것처럼 Etch 공정에서는 ‘어떻게 하면 화학적 반응을 잘 일으키는지’에 대해 초점이 맞추어져 있습니다. 그래서 Etch 공정에서는 주기율표상 7족 Halogen 가스들이 주로 사용됩니다. (F, Cl, Br)
그 이유는 7족의 할로겐 가스는 최외각 전자가 7개이기 때문에 외부에서 전자 1개만 가져와도 쉽게 안정화 됩니다. 이는 그만큼 반응성이 높다는 것을 의미합니다. 그래서 할로겐 가스를 사용할 경우 화학적 반응성이 높아 쉽게 Target 박막을 쉽게 Etching 할 수 있습니다. 예를 들어, Si을 Etching 할 경우, SiF, CF4를 주로 사용합니다.
일반적으로 모든 원자는 8개의 최외각전자를 가지기 위해 반응 또는 결합을 통해 안정화 상태에 도달합니다. 그래서 7족 원소들이 Etchant Gas로 사용되는 것입니다. 그런데, 같은 7족의 할로겐 가스라고 하더라도, 전자궤도 수가 증가하면 무거워지고, 원자 직경이 증가하여 녹는점/끓는점이 급격히 증가하게 됩니다. 이는 다시 말해, F >> Cl >> Br로 갈수록 Passivation 기능이 강해지고, Etch rate이 증가함을 의미합니다. 이는 다시 자세히 설명드리겠습니다.
8족의 Ar, Ne 등의 비활성 기체는 가장 안정적인 상태로 PVD에서 Plasma를 형성하여 Sputtering을 통한 Deposition Mechanism을 다루었습니다. 8족의 원소를 PVD에서 사용했던 것은 그만큼 Gas 자체가 안정적이기 때문에 반응성이 현저히 낮아 Sputtering 공정에서 박막을 형성할 때 화학적 반응을 최소화 시킬 수 있기 때문입니다. 그래서 Etch 공정에서는 이러한 8족 가스를 첨가가스, Ambient Gas로 사용됩니다.
Plasma Etch의 반응식을 살펴보겠습니다.
① CF4, CF4/O2, SF6, NF3 : Si+4F → SiF4 (g)
② Cl2, BCl3, SiCl4, HCl : Si+4Cl → SiCl4 (g)
③ HBr, Br2 : Si + 4Br → SiBr4 (g)
Fluorine, Chlorine, Bromine 계열의 가스가 위 반응식처럼 Si Etch에서 사용됩니다. SiF4가 형성될 경우 Boiling Point가 -86℃로 낮기 때문에 반응과 동시에 Si이 쉽게 제거가 됩니다. SiCl4는 58℃의 Boiling Point로 SiF4보다 높지만 그래도 쉽게 제거가 됩니다. 반면에 SiBr4는 BP가 154℃입니다. 따라서 F, Cl에 비해 상대적으로 쉽게 제거가 되지 않기 때문에 Br 계열 Gas로 Si Etch 시에는 외부 Annealing 처리를 통해 Etching 시 쉽게 Byproduct가 기화되면서 제거할 수 있습니다.
F를 사용하면 BP가 낮아 반응성이 상당히 크고 SiF4가 제거되면서 빠른 Etch가 가능합니다. Fluorine은 화학적 반응이 정말 활발하기 때문에 어떤 Gas로 조치를 취하지 않으면 Plasma etch에서 Chemical Etch가 지배적으로 일어나면서 ‘등방성 식각’ 특성을 가집니다. 그렇기 때문에 F 계열의 Gas만을 사용한다면, 현재의 미세공정을 위한 Narrow Vertical Profile을 구현하기 어렵습니다. Cl Gas를 사용하면 F에 비해 Etch Rate은 작아지겠지만, F에 비해 화학적 반응이 덜하기 때문에, 상대적으로 좀 더 Vertical Profile을 구현하는 것이 가능해집니다. Br은 Cl에 비해 BP가 더 높기 때문에 Si을 Etch 시 Vertical Profile 특성이 매우 우수합니다. 또한 Oxide와 쉽게 반응하지 않기 때문에 Oxide Mask를 사용하면 높은 Selectivity도 구현 가능합니다.
[꼬리 2.1]. Etch 공정시 H2 Gas를 주입하면 어떻게 되는지 설명하세요.
Plasma Etch 공정 시 Fluorine 계열의 Main Gas를 주로 사용합니다. 특히 Si을 Etch 시 Fluorine은 낮은 BP에 반응성이 매우 높아 Chemical Etch 특성이 강해지면서 등방성 식각의 Profile을 보입니다. 이는 미세화 트랜드에 적합하지 않습니다. 따라서 Fluorine의 높은 화학반응성의 장점을 살리면서 등방성 식각을 억제하는 방법은 Hydrogen, H2 Gas를 주입해줌으로써 쉽게 구현할 수 있습니다. H2 Gas를 주입하면 H가 CF4와 결합하여 HF가 형성됩니다. 즉 F의 농도가 감소하는 효과가 있습니다. 그리고 상대적으로 Carbon이 많아지면서 Carbon에 의해 형성되는 Polymer에 의해 Passivation이 일어나게 되고 F에 의한 Etch rate이 감소하게 됩니다. 그래서 반응성이 높은 Fluorine으로 Etching 시에는 등방성 식각이 일어날 수 있기 때문에 hYDROGEN 처리를 통해 Etch Rate을 낮추어 주어야 합니다.
정리하자면, F는 화학적 반응의 활성도가 매우 높기 때문에 Hydrogen 같이 외부에 주입 가스 처리를 하지 않으면, 등방성 식각이 지배적으로 일어나 Undercut과 같은 Issue가 발생하여 Vertical Profile 구현이 어렵습니다. 그래서 이를 억제하기 위해 H2 Gas를 주입하면 HF가 형성되고, 상대적으로 F에 의한 Etch Rate이 떨어지면서 Vertical Profile 구현이 가능해집니다.
2CF4 + H2 → 2CF3 + 2HF (F* 보다는 CFx 계에 의한 Etch가 증가)
[꼬리 2.2]. Etch 공정시 O2 Gas를 주입하면 어떻게 되는지 설명하세요.
Main Gas 이외에 첨가 Gas에는 O2, H2, N2, Ar, He 등이 있습니다. O2는 주로 Etch 특성을 보유할 때 동일한 Gas에 대해서 Etch 특성을 강하게 할 때 사용됩니다. CF4를 Main Etchant Gas로 사용한다고 했을 때, O2 Gas를 주입하면 Oxygen이 CF4의 Carbon과 결합하여, CO가 형성되고 그 결과 Gas 내의 F의 양이 상대적으로 증가합니다. 그래서 Fluorine, F*에 의한 화학적 Etch Rate이 증가하게 됩니다.
CF4+O2 → CF3+O2 F* → COF2 + O + 2F* (CFx 계열 보다 F*에 의한 Etch가 증가함)
[꼬리 2.3]. N2, Ar, He Gas의 역할에 대해서 설명하세요.
Plasma Etch에서 O2는 Etch Rate을 증대시키고 H2 Gas는 Etch Rate을 억제시키는 역할을 했습니다. N2, Ar, He Gas는 직접 Etch 공정시 반응에 관여하지는 않고, Gas Phase의 Chemistry를 변경하는 역할을 수행합니다. 모두가 알다시피Penning Effect는 Excitation 상태의 원자로부터 방출된 에너지에 의해 이웃한 타원자가 이온화되는 현상입니다. Penning Effect는 특히 Ar gas이 매우 높기 때문에 Plasma 공정에서 Ar이 주로 사용되는 것입니다. 그래서 방전으로 인해 Gas Phase의 전기적 특성을 변경하게 됩니다. 정리하자면 N2, Ar, He와 같은 첨가 가스는 Gas를 희석하는 용도, Plasma의 Uniformity를 높이고 Plasma의 상태를 유지하는데 필수적입니다. (Plasma에 대한 내용은 PVD를 참고)
반응형
그리드형
반도체 공정 5 : 식각 공정(Etching process) 2편
안녕하세요~~ 저번 시간에는 전반적인 식각 공정의 개요에 대해 살펴봤습니다. 이번 포스팅에서는 건식 식각과 플라즈마에 대해 중점적으로 다뤄보려고 합니다. 현재 거의 모든 반도체 공정에서는 건식 식각을 사용하고 있으며, 습식 식각은 세정 공정쪽에서 사용되는 것으로 응용되는 추세입니다. 그럼 시작할게요!
건식 식각(Dry etch)
건식 식각에는 화학적 방법과 물리적 방법이 있습니다. 화학적 방법은 플라즈마(Plasma)를 이용하고, 물리적 방법은 스퍼터링(Sputtering)을 사용합니다. 모두 증착 공정에서 다뤘던 내용입니다. 사실, 증착 공정의 기구들에서 wafer의 위치만 양극(Anode)으로 옮겨주면 식각이기 때문에 거의 비슷할 수 밖에 없어요 ㅎㅎ 그래도 식각에 초점을 두어 설명해보도록 할게요! Plasma와 Sputtering을 잘 모르신다면 아래의 링크를 참조해도 좋을 것 같습니다!
https://numong22.tistory.com/24?category=995981
화학적 방법 : 플라즈마(Plasma)
◼ 플라즈마(Plasma)는 중성입자, 라디칼, 하전입자의 집합체로, 준중성인 상태를 의미합니다.
– 중성 기체는 자연상태에 존재하는 기체로 안정된 상태입니다. 플라즈마에서 상당히 많은 부분을 차지합니다.
– 라디칼(Radical)은 반응성이 매우 좋은 중성 기체입니다. 외부에서 에너지를 흡수해 불안정한 상태입니다. 보통 반응성이 매우 큰 할로겐 족 원소를 사용합니다.
– 이온(Ion)은 중성 원자/분자에서 전자를 잃거나 얻은 상태의 대전된 입자입니다. 플라즈마 공정에서는 주로 양이온을 사용합니다.
– 전자(Electron)는 중성기체에서 방출된 전자로, 플라즈마를 유지하고, 외부 전압에 빠르게 반응하여 바이어스(bias) 특성을 결정합니다.
◼ 식각 공정에서 사용하는 플라즈마는 저온 플라즈마 입니다. 저온 플라즈마에는 백 만개(1,000,000)의 가스 분자 중 1000개 정도가 라디칼이고 1개 정도가 이온화되어 있는 상태입니다. 따라서 플라즈마에서 실제 식각(Etch) 반응을 일으키는 것은 라디칼이고, 이온은 도움을 주는 역할로 이해해야됩니다. 후에 RIE라는 식각 방법을 소개할텐데, 이는 이온을 추가로 넣어 물리적인 반응과 화학적인 반응 모두를 적용한 Etching 방법입니다.
플라즈마에서 나타나는 현상들을 설명하겠습니다.
(1) 일단 플라즈마가 생성됩니다. 자세한 현상은 위에 걸어둔 링크를 참조하시면 됩니다.
(2) 식각제(Etchant)가 생성됩니다. 이 식각제가 wafer의 표면과 반응하여 원하는 부분을 제거할 것입니다.
식각제 생성
(3) 생성된 식각제가 표면과 흡착하여 화합물을 형성합니다. surf는 표면(surface)을 뜻합니다. 형성된 화합물은 이후 표면에서 탈착되어 가스 상태가 되고, 진공 펌프에 의해 외부로 배출됩니다.
식각제 흡착과 화학반응
반응성 이온 식각(RIE : Reactive Ion Etch)
가운데가 RIE이다.
RIE (Reactive Ion Etch)는 화학적 식각(Gas phase etch) 물리적 식각(Sputtering)을 결합하여 사용하는 건식 식각입니다. 원리는 간단합니다. 플라즈마에 양이온 가스를 주입합니다. 양이온 입자들이 식각하고자 하는 표면에 충격을 주어 결합을 약하게 합니다. 결합이 약해지면 플라지마 내의 Etchant가 쉽게 표면과 반응하게 됩니다. 위 그림은 RIE의 대표적인 예로 불화 제논 (XeF2)와 아르곤 가스(Ar+)를 나타냈습니다. 왼쪽 그래프는 플라즈마만 사용했을 경우를 (순수 화학), 오른쪽 그림은 스퍼터링만 사용했을 경우 (순수 물리)의 그래프입니다. 가운데 그래프는 RIE에 해당하고, 양 옆의 그래프에 미해 식각 속도(Etch rate)가 10배 정도 증가했음을 알 수 있습니다.
RIE에서 비등방성을 높이는 방법이 있습니다. Silicon을 식각할 때 C2F6를 넣어주게 되면 Si와 반응하여 C-F Polymer를 형성하게 됩니다. 이 폴리머는 식각되는 부분의 측면과 하단부에 형성되는데, 하단부는 Sputtering으로 식각되고, 측면부에는 계속 Polymer가 쌓여 일종의 통로를 형성합니다. 즉, 측면부의 Polymer는 비등방성 식각이 이뤄지도록 하는 Suface Inhibitor의 역할을 합니다. 이 기술을 TSV (Through Silicon Via)라는 반도체 소자 내의 터널을 만들때 굉장히 유용하게 사용됩니다.
Si와 SiO2의 식각 선택비 조절
Si와 SiO2의 식각 선택비 조절에 대해 살펴보도록 하겠습니다. 아까 플라즈마로 할로겐 족 원소들을 주로 이용한다고 했습니다. 대표적으로 F와 Cl에 어떻게 반응하는지 보겠습니다.
(1) 먼저 Si는 F와 Cl에 모두 식각이 잘 됩니다. 반응은 아래와 같이 일어납니다.
골고루 잘 먹는 Si
(2) 반면, SiO2는 F에서 식각되지만, Cl에서는 식각 반응이 일어나지 않습니다.
편식하는 SiO2
◼ 따라서 Si를 식각할 때 Cl2와 같은 가스를 이용하여 산화막이 식각되지 않도록 설정할 수 있습니다. 단, Cl기의 식각 속도가 F기보다 느리기 때문에 초반에 F기로 식각하다가 산화막이 노출되면 Cl기로 바꾸어 식각을 진행해줍니다.
◼ 또한 공정에 산소가스(O2)를 넣어주면 F* (F 라디칼)이 증가하게 됩니다. F*가 증가하면 산화막이 식각되긴 하지만, Si의 식각 속도가 증폭하기 때문에 선택비를 높일 수 있습니다.
건식 식각 장비
건식 식각 장비는 주로 RF 플라즈마를 이용하여 진행합니다. RF 플라즈마는 DC 플라즈마에 비해 반도체 공정에서 굉장히 광범위하게 응용됩니다. 자세한 내용은 아래 링크를 참조하시면 될 것 같습니다.
https://numong22.tistory.com/27?category=995981
그래도 간단하게 요약하자면 다음과 같습니다.
I) RF 플라즈마의 경우 전극으로 도체와 부도체 모두 사용할 수 있지만, DC의 경우는 반드시 도체여야 합니다.
II) RF의 경우 전극이 플라즈마 내에 노출되지 않아도 방전(Discharge)이 가능하지만, DC의 경우에는 반드시 노출되어야 되므로 wafer가 오염될 가능성이 큽니다.
III) RF의 방전 이온화 효율이 일반적으로 높고, 유지 압력 또한 낮습니다.
CCP
따라서 RF 플라즈마를 형성하기 위해 CCP (Capacitor Couple Plasma)를 사용합니다. 이는 두 개의 전극이 마주보고 있는 용량 결합형 플라즈마입니다. 그러나 반도체의 집적도 증가로 인해 요구되는 선폭이 점점 좁아져 건식식각이 어려워지고 있습니다. CCP의 단점은 입사하는 이온의 양 (공정 압력)과 이온의 에너지를 독립적으로 조절할 수 없다는 것입니다.
▶ 압력을 낮춰 이온의 방향성을 개선하려고 하면, 이온의 밀도가 낮아져 식각 속도(Etch rate)가 느려지고, 이온의 에너지가 에너지가 너무 높아져 소자에 손상을 입힐 수 있습니다. 에너지가 높아지는 이유는 MFP가 커지기 때문입니다. MFP를 잘 모르시는 분들은 아래 링크를 참조하시면 될 것 같습니다.
https://numong22.tistory.com/19?category=995981
▶ 반대로 압력을 높여 식각 속도(Etch rate)를 증가하려고 하면 이온의 에너지가 낮아지고 방향성이 방해를 받아 등방성 (Isotropic) 식각이 강해집니다.
이러한 CCP의 단점을 개선하기 위해 HDP (고밀도 플라즈마 : High Density Plasma)가 개발되었다. HDP는 저압에서도 동작이 가능하며, 바이어스를 독립적으로 조절 가능한 특징이 있습니다. HDP의 종류에는 유도결합형 플라즈마 (ICP : Inductive Coupled Plasma), 헬리콘 플라즈마 (Helicon Plasma), 그리고 ECR (Electron Cyclotron Resonance) Plasma가 있습니다. 이 중 ICP가 현재 반도체 공정에서 가장 보편적으로 사용되고 있습니다. 아래의 표를 보시면 ICP는 압력이 낮아 비등방성도 좋고, 이온의 밀도가 높으므로 Etch rate가 증가합니다. 또한 에너지를 독립적으로 조절할 수 있고, 에너지가 상대적으로 작으므로 기판 손상의 영향 또한 적습니다.
CCP ICP 압력(mtorr) 50~1000 0.5~50 플라즈마 밀도(/cm^3) 10^9~10^11 10^10~10^12 이온 에너지(eV) 200~1000 20~500(조절 가능)
[반도체 특강] 식각(Etching), 패턴을 완성하다-下
초창기 식각의 습식 방식은 세정(Cleansing)이나 에싱(Ashing) 분야로 발전했고, 반도체 식각은 플라즈마(Plasma)를 이용한 건식식각(Dry Etching)이 주류로 자리잡았습니다. 플라즈마는 주로 전자와 양이온, 라디칼(Radical) 입자로 구성되는데요. 플라즈마에 가해지는 에너지는 중성 상태인 소스가스의 최외각전자를 떼어내어 양이온으로 만들고, 또 분자에서 불완전한 원자를 떼어내어 전기적으로 중성 상태인 라디칼을 만듭니다. 건식식각은 플라즈마를 구성하는 양이온과 라디칼을 이용하는데, 양이온은 이방성(한쪽 방향 식각), 라디칼은 등방성(모든 방향 식각)의 성질을 띠게 됩니다. 이때 라디칼이 양이온의 함량보다 월등히 많게 되지요. 그렇다면 건식식각이 습식식각(Wet Etching)과 같이 등방성 식각이어야 함에도 불구하고, 주로 이방성 식각으로 초미세회로를 구현할 수 있는 이유는 무엇일까요? 또 양이온과 라디칼의 경우 식각 속도가 매우 느린데, 이러한 단점을 안고 플라즈마를 양산용 식각에 어떻게 적용할 수 있을까요?
1. 종횡비(Aspect Ratio)
<그림1> 종횡비의 개념 및 Tech. 발전에 따른 종횡비 변화
종횡비(Aspect Ratio)란 종축 대비 횡축의 길이(높이/밑변의 길이)의 비율(Ratio)을 뜻합니다. 회로 선폭이 작아짐에 따라 종횡비의 값도 상승하게 되지요. 즉 종횡비(A/R)가 10일 때 밑변이 10nm이라면 높이 100nm의 참호(공극)를 식각공정에서 파내야 합니다. 따라서 초미세화(2D)나 고밀도(3D)가 요구되는 차세대 제품의 경우, 식각 시 하부 막을 양이온이 파고들어 갈 수 있을 정도의 매우 높은 종횡비를 구현해야 할 필요가 있지요.
2D에서 회로 선폭 10nm 미만의 초미세 Tech.를 구현하려면 D램의 커패시터(Capacitor) 종횡비가 100 이상을 유지해야 하고, 낸드플래시의 3D 역시 셀의 256단 적층 이상을 구현하기 위해서는 고(高)종횡비가 필요합니다. 소자나 제품기술 혹은 다른 공정기술에서 요구되는 목표를 달성했다 하더라도, 식각 공정에서 이를 받쳐주지 못하면 필요한 제품을 생산할 수 없지요. 식각 기술이 점점 중요해지는 이유입니다.
2. 플라즈마 식각 개요
<그림2> 막 종류에 따른 플라즈마 소스가스
관통관의 속이 비어 있을 경우, 관의 직경이 좁을수록 모세관현상에 의해 액체의 진입이 용이해집니다. 그러나 맨땅에 참호(막다른 골목)를 파내야 하는 경우라면 오히려 어려워지지요. 따라서 회로 선폭이 3~5㎛였던 70년대 중반부터 습식식각 대신 건식식각이 대세가 됐습니다. 즉 유기적으로 뭉쳐진 용액분자보다는, 이온화는 됐지만 개별적인 분자의 부피가 작기 때문에 깊은 참호를 침투하기가 훨씬 쉬워지지요.
플라즈마 식각에서는 먼저 식각을 진행할 프로세스 챔버(Chamber) 안을 진공으로 만든 후, 식각할 막(Layer)에 맞는 플라즈마 소스가스를 주입합니다. 막질이 탄탄한 산화막을 식각 할 때에는 강력한 C-F 계열 소스를 사용하고, 산화막보다 막질이 약한 실리콘이나 금속막에서는 CL 계열인 소스가스를사용합니다. ▶<[반도체 특강] 반도체 공정의 카운셀러, 플라즈마> 편 참고
그렇다면 게이트 막과 그 하부의 절연막(SiO2)은 어떻게 식각을 할까요?
먼저 게이트 막은 폴리실리콘의 식각선택비를 갖는 CL 계열의 플라즈마로 실리콘을 제거(Si+Cl2)한 뒤, 하부 절연막은 이산화실리콘의 막을 식각할 수 있는 선택비를 갖는 좀 더 강력한 C-F 계열로 2단계 식각(SiO2+CF4)을 합니다.
3. RIE(반응성이온식각 혹은 물리화학식각) 프로세스
<그림3> RIE 방식의 장점(이방성과 높은 식각률)
플라즈마는 등방성인 라디칼과 이방성인 양이온을 동시에 함유하고 있는데, 어떻게 이방성 식각을 진행할까요?
플라즈마를 이용한 건식식각은 대부분 RIE(Reactive Ion Etching) 방식으로 진행하거나 RIE 방식에 기반을 둔 응용방식으로 진행합니다. RIE 방식의 핵심은 이방성인 양이온으로 식각 부위를 공격해 막질 내 타깃의 분자-분자 간 결합력을 약화시킨 뒤 약해진 부위를 라디칼이 흡착, 막을 구성하는 입자와 결합해 휘발성 화합물인 가스로 만들어 배출시키는 방식입니다.
라디칼은 등방성의 성질을 띠지만, 결합력이 강한 벽면보다는 양이온의 공격으로 결합력이 약화된 바닥 면을 구성하는 분자들이 더 쉽게 라디칼에 포획돼 새로운 화합물로 변합니다. 따라서 하방 식각이 주류가 되겠지요. 포획된 입자들은 라디칼과 함께 가스화되어 표면으로부터 탈착해 떨어져 나가 진공의 힘에 의해 배출됩니다.
이때 양이온 식각 혹은 라디칼 식각을 각각 별도로 진행할 때보다, 물리적 작용을 하는 양이온과 화학적 반응을 하는 라디칼을 병합해 동시에 물리화학적 진행을 하는 경우에 식각률(Etch Rate, 시간에 따른 식각정도)이 10배 가까이 높아집니다. 이렇게 되면 이방성의 하방 식각의 식각률도 높아지면서, 식각 후 남는 폴리머도 함께 해결할 수 있게 돼 일거삼득이지요. 이를 RIE(Reactive Ion Etching, 이온작용식각)이라고 합니다. 이때 관건은 막질에 알맞은 플라즈마 소스가스를 찾는 것이라고 할 수 있습니다. ※ 플라즈마 식각이 곧 RIE 식각이므로, 동일한 개념으로 생각해도 무방합니다.
4. 식각률(Etch Rate)과 핵심 성능지수
<그림4> 식각률과 관계된 식각의 핵심 성능지수
식각률은 1분당 막을 식각해내는 참호(Hole)의 깊이를 뜻합니다. 그렇다면 한 웨이퍼 상에서 식각률이 부분별로 다르다는 것은 무엇을 의미할까요?
이는 웨이퍼 상의 지점별로 깎이는 식각의 깊이가 다르다는 것입니다. 따라서 이때 평균 식각률과 식각의 깊이를 감안해 식각을 마쳐야 하는 EOP(End of Point)를 설정하는 것이 중요합니다. EOP를 설정했더라도 부위별로 식각이 목표보다 많이 되거나(Over 식각) 덜 된(Under 식각) 부분이 생깁니다. 그래도 Over 식각이 Under 식각보다 유리합니다. Under 식각이 될 경우, 식각이 덜 된 부분이 다음 공정(예: 이온주입)을 방해하기 때문이지요.
이외에 식각률로 가늠하는 식각의 핵심 성능지수로는 선택비(Selectivity)가 있습니다. 이의 기준은 항상 마스킹 역할을 하는 막(PR막, 산화막, 질화막 등)의 식각률 대비 타깃막의 식각률로써, 선택비가 높을수록 타깃막의 식각이 빠르게 진행된다는 의미입니다. 미세화가 될수록 선택비가 높아야 패턴이 제대로 구현되지요. 양이온 식각의 선택비는 (직진성이므로) 낮지만 라디칼 식각의 선택비가 높으므로 RIE의 선택비가 높아지는 장점이 있습니다.
또한, 식각할 참호들이 몰려있는 부위보다는 참호 밀도(Loading Effect)가 낮은 부위일수록 식각이 더 원활하게 진행됩니다. Electrode(소스가스 필터기)를 빠져나온 양이온 혹은 라디칼은 밀도가 균일하게 한정돼 있는데, 참호들의 개수가 목표보다 많아지면 참호당 식각에 참여할 소스들이 부족해 충분한 깊이로 파내지 못하기 때문입니다. 따라서 한 웨이퍼 내 평판 전체와 웨이퍼와 웨이퍼 간 식각률의 균일성(Uniformity)이 매우 중요합니다. 이를 위해 Electrode를 프로세스 챔버 중간에 설치하기도 하며 제품 설계 시 회로배치를 균등하게 하려는 노력을 기울이지요.
5. 식각 프로세스
<그림5> 식각공정 프로세스
먼저 웨이퍼를 섭씨 800~1,000도로 유지되는 산화공정의 퍼네이스(Furnace, 爐) 안에 넣고 웨이퍼 표면상에 높은 절연 특성을 띄는 이산화실리콘(SiO2) 산화막을 건식 방식으로 형성합니다. 그 후 증착공정으로 이동시켜 산화막 위로 실리콘 막 혹은 도전성 막을 CVD/PVD 공정으로 만든 다음, 실리콘막일 경우 필요 시 불순물을 확산시켜 도전성을 높여줍니다. 확산 진행 시에는 여러 불순물을 반복적으로 투입하기도 합니다. ▶ <[반도체 특강] 게이트 및 게이트 옥사이드층 만들기> 편 참고
이제 절연막과 폴리막을 합쳐 식각을 해야 하는데, 먼저 포토공정에서 PR(Photo Resist, 감광액)을 코팅합니다. 그다음 PR막 위에 마스크를 올려놓고 이머젼(Immersion) 방식으로 습식노광을 하면 원하는 패턴이 PR막 위에 새겨지지요(육안으로는 보이지 않습니다). 패턴의 윤곽을 드러내기 위해 현상을 하면 감광된 부위의 PR이 제거됩니다. 그리고 포토공정을 마친 웨이퍼를 식각공정으로 옮겨 건식식각을 실시합니다. ▶ <[반도체 특강] 포토(Photo) 공정 下편-노광(Exposure)과 현상(Develope)>편 참고
건식식각은 주로 RIE 방식으로 진행하는데, 막별로 소스가스를 바꿔가며 반복 진행합니다. D램의 커패시터를 형성할 때는 ALD(Atomic Layer Deposition) 공정의 단차피복성(Step Coverage, 수평의 바닥 면과 수직 벽면의 두께가 고르게 증착되는지를 나타내는 비율)를 높이기 위해 여러 번 증착과 식각공정을 섞어 진행하듯, 이번에는 반대 방향으로 식각의 종횡비를 높이기 위해 건식식각과 습식식각을 섞어서 진행합니다. 또, 중간중간 세정을 통해 참호(식각으로 형성된 공극, Hole) 밑바닥에 쌓여있는 폴리머(Polymer)를 제거합니다. 중요한 것은 세정용액이나 플라즈마 소스들이 참호 밑바닥까지 내려갈 수 있도록 재질/소스/시간/형태/순서 등 모든 변수를 총동원해 유기적으로 맞춰야 합니다. 그중 변수가 한가지라도 생기면 그에 따라 다른 변수들도 다시 계산해 맞춰 놓아야 하며, 단계별 목적에 부합할 때까지 여러 번 수행하지요.
RIE(Reactive Ion Etching)에 대해 알아보기(feat. 플라즈마의 원리)
안녕하세요 Jista입니다.
오늘은 Reactive Ion Etching에 대해 알아보겠습니다. 플라즈마의 개념을 알아야해서 살짝 어렵더라구요.
그래서 RIE에 대해 알기전 플라즈마에 관해 간략히 설명을 드릴게요.
플라즈마는 제 4의 물질로 알려져있습니다. 아마 고등학교때까지는 모든 물체가 고체,액체,기체로만 이루어져있다고 배웠을겁니다. 하지만 기체에 아주 강한 에너지를 가해주면 플라즈마 상태라는 것이 생깁니다.
위 그림을 보시면 고체에 에너지(혹은 열)을 가하면 분자사이의 몇몇 결합이 끊어져 액체가 됩니다.
마찬가지로 액체에 에너지를 가하면 분자사이의 결합이 끊어져 기체가 됩니다. 이때까지만 해도 +와 -는 원자에 속해있기 때문에 원자 하나하나 개별로 봐도, 전체적(원자들의 집단)으로 봐도 중성입니다.
액체에 강한 에너지를 가하면 제4의 물질인 플라즈마가 됩니다. 하지만 플라즈마는 고체, 액체, 기체와는 다른 큰 차이점이 있습니다.
바로 양성자와 전자가 분리된다는 점인데요.
우리가 아는 원자는 이렇게 양성자,중성자 주위를 전자가 도는 구조입니다. 고체, 액체, 기체 그림을 보셔도 초록색 +와 초록색 -가 원안에 ‘같이’ 있습니다. 하지만 액체에 강한 에너지를 가하게되면 더 이상 원자간에 끊어질 결합이 없어서 양성자와 전자의 관계가 끊어집니다.
그림1의 플라즈마를 보시면 양성자(주황색 원)와 전자(검정색 원) 이 나뉘어져있죠? 고체, 액체, 기체에서는 둘이 붙어있었다 이겁니다. 그러나 너무 많은 힘을 가하다보니 이젠 양성자와 전자까지 따로 분리되는 상태가 된거에요. 이게 바로 플라즈마 입니다. 플라즈마상태인 전자의 수가 많아지면(따로 노는 전자가 많아지면), Random하게 움직이던 전자가 일사분란하게 같은 방향으로 움직이는 전자로 바뀝니다.(바닷속 물고기 같은 느낌)
전자의 뭉치는 성질을 그림1의 플라즈마 부분에 표현해봤습니다. 국부적(local,일부분)으로 보면 왼쪽 위는 전자가 더 많은 – , 오른쪽 아래는 양성자가 더 많은 +를 띄게 됩니다. 하지만 전체적(파랑색 사각형)으로 보면 양성자 수와 전자 수가 같기 때문에 중성을 띄게 됩니다.
Reactive Ion Etching(이하 RIE)는 보통 Fluorine(F)에 13.56MHz(Radio Frequency)를 가해서 플라즈마 이온으로 만듭니다.(다른 frequency도 가능하지만 13.56MHz가 제일 좋은 성능을 냈다함) 엄청 빠른 라디오 주파수의 에너지를 F에 가하는 것이죠. RF를 가하면 전자와 양성자는 빠른 frequency를 따라가지 못해서 서로 분리가 됩니다.
RIE를 이용하는 챔버내의 기본 구조 그림입니다. 1번과 4번처럼 전극(electrode)을 놔두고 5번(분홍색)에 etching할 substrate나 sample을 배열합니다. 2번 영역은 플라즈마 영역으로 전체적으로 보면 중성입니다. 위쪽에 -, 아래쪽에 +를 걸어줬기 때문에 플라즈마 이온중 F- 이온이 인력 및 전기장에 의해 아래로 빠르게 돌진합니다.
이 F- 이온은 substrate에 강하게 부딪혀 physical etching인 sputtering을 일으키거나 chemical etching인 ‘substrate속 원자과 결합한 뒤 분산’ 을 일으킵니다.
보통 sputtering같은 경우는 위에서 아래로 빠르게 움직여서 부딪히니까 발생하잖아요. 방향성을 띈다는 의미입니다. 그렇기 떄문에 Anisotropic(이방성)을 띄며 etching이 됩니다. 한마디로 옆으로는 etching이 느리게 되고 아래로는 etching이 빠르게 된다는 의미입니다.
chemical etching은 기판의 원자와 결합한 뒤 떨어져 나가는 반응이라 방향성을 띄지 않습니다. 그렇기 때문에 어느 방향으로든 비슷한 속도로 etching이 되는 Isotropic(등방성)을 띄며 etching이 됩니다.
위 그림은 원하는 region만 etching을 시키기 위해 barrier로 photoresist를 덮어놓은 그림입니다.
RIE 실험 결과 정리 포스팅
RIE에 관한 실험 결과들을 정리해놓은 문헌입니다.
Oxide와 Ar의 영향, Si3N4 SiO2 Si 같은 물질에 따라 RIE가 어떻게 일어나는지 적어놨어요~
Reactive Ion Etching
Reactive Ion Etching (RIE) uses a combination of chemical and physical reactions to remove material from a substrate; it is the simplest process that is capable of directional etching. A highly anisotropic etching process can be achieved in RIE through the application of energetic ion bombardment of the substrate during the plasma chemical etch. The RIE process thus provides the benefits of highly anisotropic etching due to the directionality of the ions bombarding the substrate surface as they get accelerated towards the negatively biased substrate, combined with high etch rates due to the chemical activity of the reactive species concurrently impinging on the substrate surfaces. The synergistic effect of ion bombardment on increased etch rates in the presence of chemically active species was first demonstrated and explained by Coburn and Winters, where they showed the significantly higher silicon etch rate in the presence of both Ar+ ion beam and XeF 2 gas compared to either the Ar+ ion beam or the XeF 2 gas only as illustrated in Figure 1. In the RIE process, the ions carry sufficient energy to break the chemical bonds of the atoms in the substrate that they impinge upon lowering the activation energy for the chemical etching reactions and thus increasing the reaction rates with the reactive neutrals that are also incident on the substrate surface. In certain etching chemistries, there may be reaction byproducts that are formed on the surface and act as inhibitors for the chemical etch processes. The energetic ions also act to remove such reaction byproducts from the surface through physical sputtering exposing the underlying material to be removed by the chemically reactive species. Thus RIE is sometimes also referred as Ion-Enhanced Etching or Reactive and Ion Etching. The highly directional nature of ions bombarding the surfaces leads to the anisotropy in the etch process as illustrated in the Figure 2.
Reactive-ion etching
Method used to relatively precisely remove material in a controlled and fine fashion
A commercial reactive-ion etching setup in a cleanroom
Reactive-ion etching (RIE) is an etching technology used in microfabrication. RIE is a type of dry etching which has different characteristics than wet etching. RIE uses chemically reactive plasma to remove material deposited on wafers. The plasma is generated under low pressure (vacuum) by an electromagnetic field. High-energy ions from the plasma attack the wafer surface and react with it.
Equipment [ edit ]
A typical (parallel plate) RIE system consists of a cylindrical vacuum chamber, with a wafer platter situated in the bottom portion of the chamber. The wafer platter is electrically isolated from the rest of the chamber. Gas enters through small inlets in the top of the chamber, and exits to the vacuum pump system through the bottom. The types and amount of gas used vary depending upon the etch process; for instance, sulfur hexafluoride is commonly used for etching silicon. Gas pressure is typically maintained in a range between a few millitorr and a few hundred millitorr by adjusting gas flow rates and/or adjusting an exhaust orifice.
Other types of RIE systems exist, including inductively coupled plasma (ICP) RIE. In this type of system, the plasma is generated with a radio frequency (RF) powered magnetic field. Very high plasma densities can be achieved, though etch profiles tend to be more isotropic.
A combination of parallel plate and inductively coupled plasma RIE is possible. In this system, the ICP is employed as a high density source of ions which increases the etch rate, whereas a separate RF bias is applied to the substrate (silicon wafer) to create directional electric fields near the substrate to achieve more anisotropic etch profiles.[1]
Method of operation [ edit ]
A diagram of a common RIE setup. An RIE consists of two electrodes (1 and 4) that create an electric field (3) meant to accelerate ions (2) toward the surface of the samples (5).
Plasma is initiated in the system by applying a strong RF (radio frequency) electromagnetic field to the wafer platter. The field is typically set to a frequency of 13.56 Megahertz, applied at a few hundred watts. The oscillating electric field ionizes the gas molecules by stripping them of electrons, creating a plasma.
In each cycle of the field, the electrons are electrically accelerated up and down in the chamber, sometimes striking both the upper wall of the chamber and the wafer platter. At the same time, the much more massive ions move relatively little in response to the RF electric field. When electrons are absorbed into the chamber walls they are simply fed out to ground and do not alter the electronic state of the system. However, electrons deposited on the wafer platter cause the platter to build up charge due to its DC isolation. This charge build up develops a large negative voltage on the platter, typically around a few hundred volts. The plasma itself develops a slightly positive charge due to the higher concentration of positive ions compared to free electrons.
Because of the large voltage difference, the positive ions tend to drift toward the wafer platter, where they collide with the samples to be etched. The ions react chemically with the materials on the surface of the samples, but can also knock off (sputter) some material by transferring some of their kinetic energy. Due to the mostly vertical delivery of reactive ions, reactive-ion etching can produce very anisotropic etch profiles, which contrast with the typically isotropic profiles of wet chemical etching.
Etch conditions in an RIE system depend strongly on the many process parameters, such as pressure, gas flows, and RF power. A modified version of RIE is deep reactive-ion etching, used to excavate deep features.
See also [ edit ]
키워드에 대한 정보 reactive ion etching 공정
다음은 Bing에서 reactive ion etching 공정 주제에 대한 검색 결과입니다. 필요한 경우 더 읽을 수 있습니다.
이 기사는 인터넷의 다양한 출처에서 편집되었습니다. 이 기사가 유용했기를 바랍니다. 이 기사가 유용하다고 생각되면 공유하십시오. 매우 감사합니다!
사람들이 주제에 대해 자주 검색하는 키워드 Etching Silicon with Plasma – Reactive Ion Etching (RIE)
- 동영상
- 공유
- 카메라폰
- 동영상폰
- 무료
- 올리기
Etching #Silicon #with #Plasma #- #Reactive #Ion #Etching #(RIE)
YouTube에서 reactive ion etching 공정 주제의 다른 동영상 보기
주제에 대한 기사를 시청해 주셔서 감사합니다 Etching Silicon with Plasma – Reactive Ion Etching (RIE) | reactive ion etching 공정, 이 기사가 유용하다고 생각되면 공유하십시오, 매우 감사합니다.